Questo appendiabiti fai da te è costruito interamente con legno di recupero, curando, come si conviene, l’aspetto estetico, la correttezza delle geometrie e la precisione dei dettagli, per essere utilizzato in casa
Anche se gli stender appendiabiti sono reperibili in mille fogge e dimensioni, capita che quello giusto per lo spazio di cui si dispone non esista. Ecco il progetto di un appendiabiti fai da te su misura per lo spazio fra un armadio e la parete a fianco. Le dimensioni obbligate sono due, perché deve essere largo tanto da entrare senza difficoltà, ma anche lungo quel tanto da non fuoriuscire dalla sagoma dell’armadio.
Presa la decisione di usare il legno come materiale da costruzione, si individua fra gli scarti di un precedente lavoro una bella tavola di faggio sufficientemente grande per ricavare tutti i listelli necessari; questi servono per realizzare due telai laterali a forma triangolare, che vengono poi uniti mediante tre bastoni ricavati da un lungo manico di rastrello, perfettamente diritto.
Un ripiano con sponde è utilissimo e non solo per riporre oggetti, ma anche per rendere più robusta la struttura portante, essendo fissato in posizione intermedia, fra i montanti. Tutte le giunzioni fra i pezzi sono fatte con colla vinilica e rinforzate da spine di faggio passanti. La finitura è al naturale, con olio. Lo stender si sposta facilmente grazie a quattro rotelle pivotanti, applicate sotto i montanti.
Giunzione con spine passanti
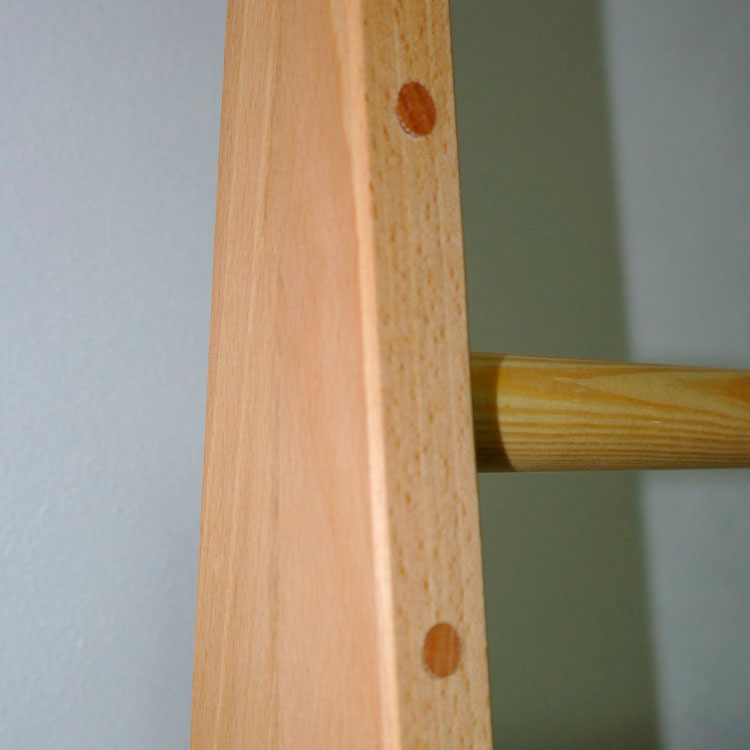
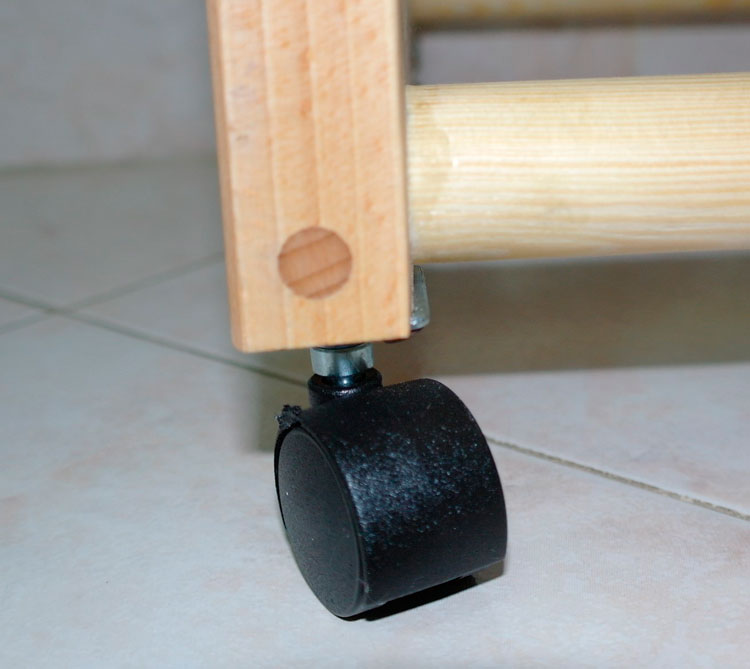
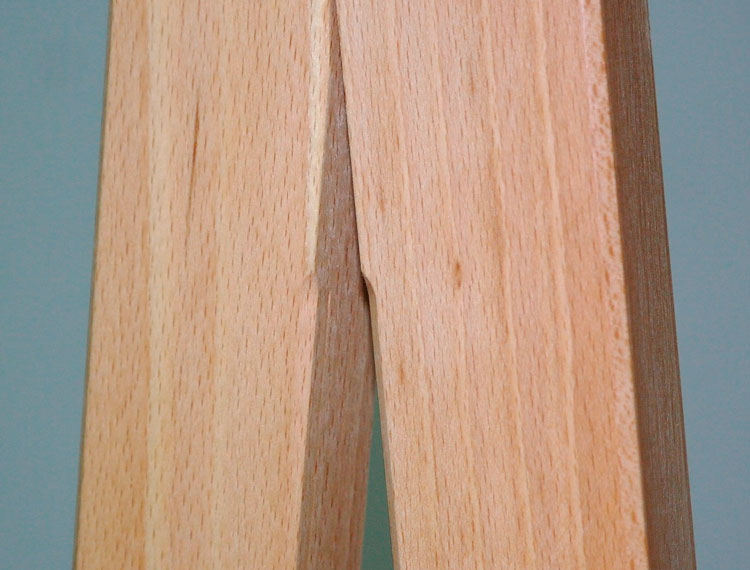
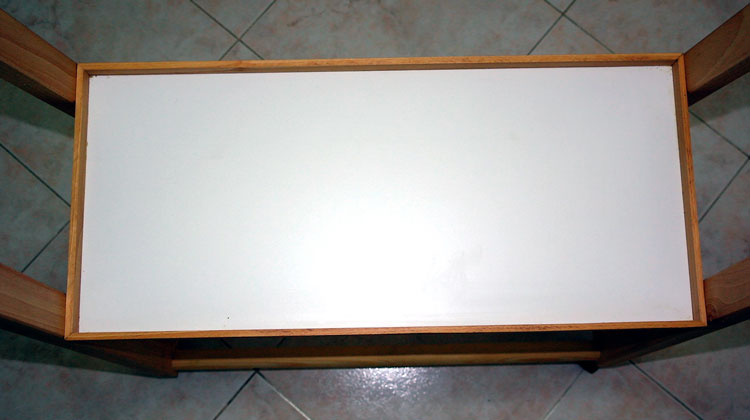
Appendiabiti fai da te stender: tutti i pezzi ricavati da una tavola
Tempo richiesto: 1 giorno
- Legno come principale materiale di costruzione
Per gran parte della costruzione dell’appendiabiti fai da te è stata usata una tavola di faggio lunga 2000 mm, larga 250 mm e spessa 30 mm.
- Ricavare i quattro listelli
I quattro listelli ricavati piallandola e tagliandola per lungo sono risultati di sezione 40×25 mm. In seguito, tutti ancora troncati alla lunghezza di 1600 mm.
- Tracciare le linee e l’angolo di taglio
Su un ampio piano di lavoro si stende qualche striscia di nastro maschera, per poter tracciare dei riferimenti circa l’inclinazione ideale dei montanti. Appoggiandoli uno per volta sulle due posizioni stabilite, si riportano alle estremità alte le linee per effettuare il taglio con l’angolo corretto e ottenere un profilo corrispondente alla tracciatura.
- Effettuare i tagli
I disegni di riferimento sul piano permettono di tracciare l’angolatura corretta dei tagli inclinati che vanno eseguiti alla base dei montanti, in modo che ci sia la planarità d’appoggio sul pavimento, e alle estremità delle due traverse, che uniscono i montanti sullo stesso lato. I tagli si effettuano con una sega giapponese.
- Unire le due coppie di montanti e le relative traverse
Approfittando sempre dell’ampio piano d’appoggio, liscio e regolare, si uniscono le due coppie di montanti e le relative traverse. Si usa colla vinilica, mettendoli in pressione con morsetti a vite. Notare che per premere correttamente le estremità dei montanti sono stati utilizzati gli scarti del taglio effettuato sugli stessi, per dar loro l’inclinazione a V rovesciata; in questo modo i morsetti lavorano in piano ed esercitano pressione senza scivolare via.
- Stabilire la dimensione del ripiano centrale
Con i due telai laterali pronti si può stabilire la dimensione del ripiano e, di conseguenza tagliare il pannello di truciolare nobilitato, spesso 18 mm, e i quattro listelli di faggio, sezione 10×25 mm, che gli vanno applicati, previa troncatura a 45° delle estremità.
- Incollare le sponde al ripiano
Per l’incollaggio delle sponde al ripiano si applica una nutrita serie di strettoi a vite, messi nelle due direzioni, per un’azione congiunta.
- Inserire le spine per una maggiore robustezza
Oltre alla colla, per ottenere la massima robustezza dell’insieme, nelle zone di giunzione si applicano alcune spine passanti. Due si mettono all’apice dei telai triangolari, dove convergono i montanti. Immobilizzato un telaio sul piano di lavoro, si effettuano due fori con il trapano, montando una punta da legno di diametro 8 mm. Un foro si fa a 50 mm dall’apice e uno a 120 mm. In ogni foro si inserisce un pezzo di tondino di faggio di diametro 8 mm, spalmato di adesivo vinilico e si taglia lasciando un moncone di abbondanza.
- Smussare gli angoli
Si monta sulla fresatrice una fresa per bisellare a 45° e si passano gli spigoli dei due telai triangolari, prima su un lato e poi sull’altro.
- Marcare il punto dove effettuare il foro del bastone
Applicando una breve striscia di nastro per mascheratura sul lato interno dei telai, si marca con molta precisione il punto dove effettuare il foro del bastone, tenendo conto che i fori devono essere eseguiti alla stessa distanza dall’estremità. Il nastro di carta serve per poter marcare liberamente il legno, senza tracciare su di esso segni che poi debbano essere cancellati.
- Forare i due telai
Il foro per il bastone sommitale si esegue con una punta Forstner montata sul trapano a colonna, fondamentale questo modo di procedere per riuscire a mantenere la perpendicolarità rispetto alla faccia laterale del telaio. Il diametro in questo caso è di 27 mm e corrisponde a quello del bastone che si è deciso di utilizzare.
- Fissare i tre bastoni
Il fissaggio dei bastoni, tre in tutto, va fatto in contemporanea, spalmando adesivo su entrambe le estremità di ognuno e mettendo in pressione tutto l’insieme. L’accortezza è quella di fare tutto questo con squadre di legno autocostruite che assicurino il mantenimento dello squadro (90°) fra montanti e bastoni, su entrambi i lati.
- Applicare le spinde per il ripiano centrale
Ormai l’appendiabiti fai da te stender sta in piedi da solo. Con due morsetti a molla per parte si tengono in posizione due listelli di legno, messi in bolla all’altezza giusta, in modo che possano sostenere il ripiano intermedio. Si effettuano i fori per applicare le spine passanti, che vanno a prendere nello spessore del ripiano. La finitura del manufatto è fatta con olio di Tung, previo passaggio con carta abrasiva a grana 220. Applicate le quattro ruote pivotanti sotto i montanti, l’appendiabiti è pronto per essere utilizzato.
Progetto di Fabrizio Uliana