Indice dei contenuti
Un attaccapanni da terra, realizzato con bracci mobili, una mensola portacappelli e una pedana poggiascarpe
La realizzazione di un attaccapanni da terra è una soluzione funzionale per l’ingresso di casa. Si tratta di un appendiabiti con bracci girevoli sull’asta portante con due mensole e una barra orizzontale che aumentano ulteriormente lo spazio a disposizione per riporre abiti, scarpe e borse senza fare disordine. Il tutto si può realizzare anche da soli e non richiede materiali costosi.
Ecco un oggetto costruito con un metodo differente rispetto ai soliti, classici appendiabiti.
Cosa occorre
Gli utensili: Seghetto alternativo, sega manuale, trapano con sega a tazza.
I materiali: truciolare nobilitato da 19 mm; bordo termoadesivo; 2 barre filettate Ø 12 mm lunghe 1000 mm; 1 manicotto filettato; tubo in PVC Ø 30 mm; 6 raccordi a T in PVC Ø 30 mm; 1 gomito in PVC Ø 30 mm; 4 rondelle Ø 12-30 mm con controdado; 5 pomoli Ø interno 30 mm; 1 piedino in gomma; colla; vernice; 4 mensole a scomparsa.
Installare l’appendiabiti da terra
Le due mensole si realizzano da piani in truciolare nobilitato, tagliandoli da un lato a semicerchio mediante il seghetto alternativo. Si rifiniscono con nastro termoadesivo per i bordi evidenti. Sul bordo lato a muro sono invece forate per inserirvi gli appositi reggimensola a scomparsa. Vanno forate anche in corrispondenza del bastone verticale, utilizzando la sega a tazza.
- Trapano a colonna PBD 40 per una foratura precisa e un impiego semplice
- Agevole esecuzione di forature in serie, grazie all’indicatore digitale, che consente di leggere con facilità l’esatta profondità di foratura
- Con laser integrato per forature precise e minitorcia a LED per una buona illuminazione dell’area di lavoro
- Preciso posizionamento del pezzo in lavorazione, grazie alla guida parallela e all’ampio piano di lavoro; mediante l’apposito morsetto rapido, potrete fissare anche pezzi a sezione circolare
- Dotazione PBD 40, guida parallela, morsetti di fissaggio rapido e confezione in cartone
- sega a tazza BIM per l'uso su legno, metallo, plastica, pannelli isolanti e per costruzioni a secco (ad es. cartongesso e OSB)
- dente alternato progressivo in acciaio super rapido (HSS), fori di espulsione grandi, codolo esagonale con Ø 9,5 mm
- disponibile con diversi diametri; profondità di taglio 40 mm per numerosi progetti di lavori interni e di carpenteria leggera
- Seghetto alternativo PST 900 PEL precisione in tutti i materiali
- Vibrazioni minime, grazie al sistema Low Vibration Bosch, con compensazione lineare delle masse ed impugnatura ergonomica con rivestimento Softgrip
- La funzione soffiatrucioli attivabile separatamente e il LED integrato PowerLight garantiscono una chiara visuale sulla linea di taglio
- Sistema SDS Bosch azionabile con una sola mano, per sostituire la lama in modo sicuro e in pochi secondi, senza l’uso di attrezzi
- Dotazione lama Speedline Wood T 144 D, sistema CutControl, dispositivo antistrappo, alloggiamento portalame, copertura di protezione trasparente e valigetta
- SEGHETTO AD ARCO 300MM - Seghetto a mano multifunzione per LEGNO e METALLO: per il taglio preciso di metallo, alluminio, metalli teneri, plastica, piccoli tagli di legno, cartongesso. Seghetto robusto: resiste a una tensione della lama di 100 kg e garantisce un risultato di taglio pulito e preciso
- COSA RICEVI alla consegna: 1 Seghetto con 2 lame distinte: 1 lama da 300 mm Bi-METALLO (24 denti/pollice) e 1 lama per LEGNO 65 Mn – da 300 mm.
- COMODO RAPIDO E UNIVERSALE: Seghetto con comoda impugnatura antiscivolo con manopola per regolazione della lama a 45 °. Taglio dritto veloce e sicuro anche per il ferro e metalli
- CAMBIO LAMA ULTRA SEMPLICE Le lame si sostituiscono in un attimo. Entrambe sono regolabili con un angolo di taglio di 45 °, in modo da poter modificare i giunti degli angoli
- Lame di ricambio: qui https://www.amazon.it/dp/B0849R7MLF e qui: https://www.amazon.it/dp/B0849RCWN7
Sul ripiano inferiore è possibile incollare un piano di protezione in gomma o linoleum, per appoggiare le scarpe. Per quanto riguarda l’appendiabiti, si possono acquistare i componenti in acciaio cromato o può essere realizzato con tubi in PVC inseriti su un’anima metallica, che va rifinita con smalto acrilico e incollando i pomoli alle barre orizzontali.
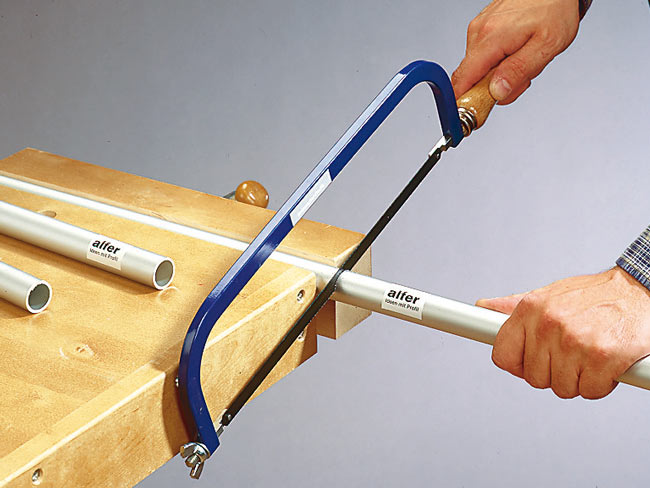
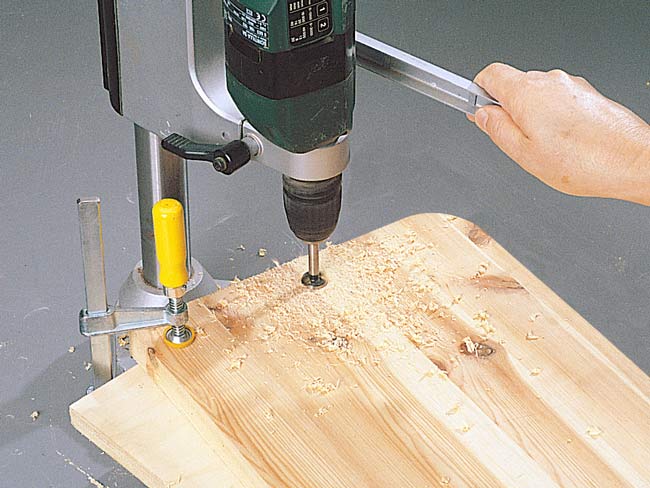
L’assemblaggio dell’attaccapanni da terra avviene seguendo il disegno successivo.